-
Table of Contents
- Introduction
- Supplier Quality Management in UAE Construction: Legal Framework and Best Practices
- Establishing Clear Quality Standards for Suppliers in UAE Construction Projects
- Auditing and Monitoring Supplier Performance for Quality Compliance
- Contractual Obligations for Quality Assurance in UAE Construction
- Supplier Qualification and Evaluation for Quality Compliance
- Risk Assessment and Mitigation Strategies for Supplier Quality Issues
- Continuous Improvement and Supplier Development for Quality Enhancement
- The Role of Technology in Ensuring Supplier Quality Compliance
- Legal Consequences of Non-Compliance with Quality Standards in UAE Construction
- Best Practices for Collaboration and Communication with Suppliers for Quality Assurance
- Q&A
- Conclusion
Ensuring Quality Compliance from Suppliers: Adhering to UAE Construction Law
Introduction
**Ensuring Quality Compliance from Suppliers According to UAE Construction Law**
In the United Arab Emirates (UAE), the construction industry is governed by a comprehensive legal framework that places significant emphasis on quality compliance. Suppliers play a crucial role in ensuring the quality of construction projects, and the UAE construction law provides a robust framework for holding them accountable for meeting quality standards. This introduction will provide an overview of the key provisions of the UAE construction law that relate to quality compliance from suppliers, highlighting the responsibilities of suppliers and the mechanisms for enforcing compliance.
Supplier Quality Management in UAE Construction: Legal Framework and Best Practices
**Ensuring Quality Compliance from Suppliers: UAE Construction Law**
In the UAE construction industry, ensuring quality compliance from suppliers is paramount for project success. The UAE construction law provides a robust legal framework to safeguard quality standards and protect the interests of all stakeholders.
**Legal Framework**
The UAE Federal Law No. 2 of 2016 on Construction Contracts (the “Construction Law”) sets out clear obligations for suppliers to comply with quality standards. Article 14 of the Construction Law requires suppliers to provide materials and equipment that meet the specifications and standards agreed upon in the contract. Failure to comply can result in penalties, including fines and contract termination.
**Best Practices**
Beyond the legal requirements, construction companies can implement best practices to enhance supplier quality compliance. These include:
* **Supplier Qualification:** Conduct thorough due diligence on potential suppliers to assess their capabilities, experience, and quality control systems.
* **Clear Contractual Agreements:** Define quality standards, inspection procedures, and acceptance criteria in detail in the supply contract.
* **Regular Inspections:** Establish a rigorous inspection regime to verify the quality of materials and equipment before acceptance.
* **Supplier Performance Monitoring:** Track supplier performance against quality metrics and take corrective actions as needed.
* **Supplier Training and Development:** Provide training and support to suppliers to improve their quality management practices.
**Benefits of Quality Compliance**
Ensuring quality compliance from suppliers offers numerous benefits for construction projects:
* **Reduced Defects and Rework:** High-quality materials and equipment minimize the risk of defects and costly rework, saving time and resources.
* **Enhanced Project Performance:** Quality-compliant suppliers contribute to the overall performance of the project, ensuring timely completion and meeting client expectations.
* **Improved Safety:** Quality materials and equipment enhance safety on construction sites, reducing the risk of accidents and injuries.
* **Reputation Protection:** Construction companies that prioritize supplier quality compliance build a reputation for delivering high-quality projects, attracting clients and investors.
**Conclusion**
The UAE construction law provides a solid legal framework for ensuring quality compliance from suppliers. By implementing best practices, construction companies can further enhance supplier quality and reap the benefits of reduced defects, improved project performance, enhanced safety, and reputation protection. By adhering to these principles, the UAE construction industry can continue to deliver world-class projects that meet the highest standards of quality and safety.
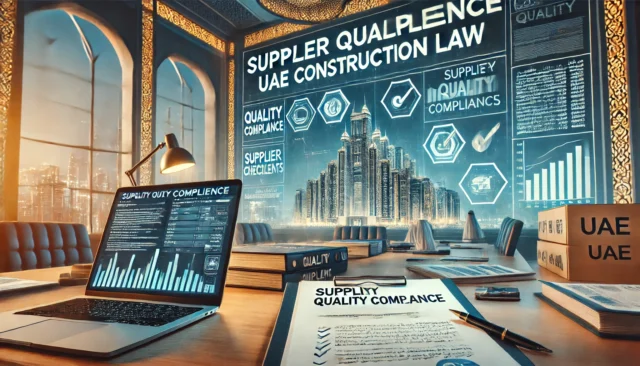
Establishing Clear Quality Standards for Suppliers in UAE Construction Projects
Ensuring quality compliance from suppliers is paramount in the construction industry, particularly in the United Arab Emirates (UAE), where stringent regulations govern construction projects. Adhering to these regulations is crucial for ensuring the safety, durability, and overall quality of buildings and infrastructure.
The UAE construction law outlines specific requirements for suppliers to meet quality standards. These requirements encompass various aspects, including the use of certified materials, adherence to industry best practices, and compliance with environmental regulations. Suppliers must demonstrate their commitment to quality by obtaining relevant certifications and implementing robust quality control systems.
Establishing clear quality standards is the cornerstone of ensuring compliance. Construction contracts should clearly define the quality expectations for materials, products, and services. These standards should be based on industry norms, international standards, and the specific requirements of the project. Suppliers should be provided with detailed specifications and drawings that outline the required quality levels.
Regular inspections and testing are essential for verifying compliance. Independent third-party inspectors can be engaged to conduct thorough inspections of materials and products before they are incorporated into the construction process. Testing can be performed to ensure that materials meet the specified performance criteria. Suppliers should be required to provide documentation demonstrating the results of inspections and tests.
In addition to inspections and testing, suppliers should be subject to regular audits. Audits can assess the supplier’s quality management system, manufacturing processes, and overall compliance with quality standards. Audits can identify areas for improvement and help suppliers enhance their quality practices.
Collaboration between contractors and suppliers is crucial for ensuring quality compliance. Contractors should work closely with suppliers to establish clear expectations, provide technical support, and monitor performance. Suppliers should be encouraged to participate in project planning and design reviews to ensure that their products and services meet the project’s specific requirements.
By implementing these measures, construction companies in the UAE can ensure that their suppliers meet the highest quality standards. This will not only enhance the quality of construction projects but also reduce the risk of defects, delays, and costly rework. Ultimately, it will contribute to the development of a safe, sustainable, and high-quality built environment in the UAE.
Auditing and Monitoring Supplier Performance for Quality Compliance
**Ensuring Quality Compliance from Suppliers: A Legal Imperative in UAE Construction**
In the dynamic construction industry of the United Arab Emirates (UAE), ensuring quality compliance from suppliers is paramount to safeguarding project integrity and public safety. The UAE construction law places a significant emphasis on quality control, outlining stringent regulations that govern the procurement and utilization of materials and services.
To comply with these regulations, contractors must establish robust supplier performance monitoring systems that assess and verify the quality of goods and services provided by their suppliers. This process involves a comprehensive evaluation of suppliers’ capabilities, including their technical expertise, production processes, and quality management systems.
The UAE construction law mandates that contractors conduct regular audits of their suppliers to ensure ongoing compliance with quality standards. These audits should cover all aspects of the supplier’s operations, from raw material sourcing to manufacturing and delivery. By conducting thorough audits, contractors can identify potential quality issues early on and take corrective actions to mitigate risks.
In addition to audits, contractors should also implement robust monitoring mechanisms to track supplier performance over time. This can involve establishing key performance indicators (KPIs) that measure the quality of materials and services, as well as the supplier’s responsiveness and reliability. By monitoring these KPIs, contractors can identify suppliers who consistently meet or exceed expectations and those who require improvement.
Furthermore, contractors should maintain detailed records of all supplier interactions, including audit reports, performance evaluations, and corrective action plans. These records serve as evidence of the contractor’s due diligence in ensuring quality compliance and can be used to demonstrate compliance with the UAE construction law.
By adhering to these legal requirements and implementing effective supplier performance monitoring systems, contractors can mitigate the risks associated with poor-quality materials and services. This not only ensures the safety and durability of construction projects but also protects contractors from potential legal liabilities and reputational damage.
In conclusion, ensuring quality compliance from suppliers is a critical aspect of construction project management in the UAE. By conducting regular audits, implementing performance monitoring mechanisms, and maintaining detailed records, contractors can fulfill their legal obligations and safeguard the quality of their projects. This proactive approach not only enhances project outcomes but also contributes to the overall reputation and success of the construction industry in the UAE.
Contractual Obligations for Quality Assurance in UAE Construction
**Ensuring Quality Compliance from Suppliers: UAE Construction Law**
In the UAE construction industry, ensuring quality compliance from suppliers is paramount to project success. The UAE construction law provides a robust framework for contractors to safeguard the quality of materials and services procured from suppliers.
Firstly, contractors must establish clear quality standards in their contracts with suppliers. These standards should specify the required performance, specifications, and testing procedures. By incorporating these standards into the contract, contractors can hold suppliers accountable for meeting the agreed-upon quality levels.
Secondly, contractors should conduct thorough supplier evaluations before awarding contracts. This involves assessing the supplier’s track record, financial stability, and technical capabilities. By selecting reputable and qualified suppliers, contractors can minimize the risk of receiving substandard materials or services.
Thirdly, contractors must implement a robust quality control system to monitor and verify the quality of materials and services received from suppliers. This system should include regular inspections, testing, and documentation. By proactively monitoring quality, contractors can identify and address any potential issues early on, preventing costly rework or delays.
Furthermore, contractors should establish clear communication channels with suppliers to facilitate the exchange of information and feedback. Regular meetings, site visits, and progress reports can help contractors stay informed about the supplier’s performance and address any concerns promptly.
In addition to contractual obligations, contractors should also consider the following best practices to enhance quality compliance from suppliers:
* **Establish a supplier quality management program:** This program should outline the contractor’s expectations, quality standards, and supplier evaluation criteria.
* **Provide training and support to suppliers:** By educating suppliers on the contractor’s quality requirements, contractors can improve their understanding and adherence to the standards.
* **Foster a collaborative relationship with suppliers:** By working closely with suppliers, contractors can build trust and encourage them to prioritize quality.
* **Implement a continuous improvement process:** Regularly reviewing and updating quality standards and procedures ensures that the contractor’s quality assurance system remains effective and aligned with industry best practices.
By adhering to the UAE construction law and implementing these best practices, contractors can effectively ensure quality compliance from suppliers, safeguarding the quality of their construction projects and minimizing the risk of costly defects or delays.
Supplier Qualification and Evaluation for Quality Compliance
**Ensuring Quality Compliance from Suppliers: A Legal Imperative in UAE Construction**
In the dynamic construction industry of the United Arab Emirates (UAE), ensuring quality compliance from suppliers is paramount to safeguarding project integrity and public safety. The UAE construction law places significant emphasis on supplier qualification and evaluation to guarantee that materials and services meet the highest standards.
The law mandates that contractors conduct thorough due diligence on potential suppliers before awarding contracts. This involves assessing the supplier’s technical capabilities, financial stability, and quality management systems. Contractors must verify that suppliers possess the necessary certifications, licenses, and accreditations to ensure compliance with industry regulations and standards.
Furthermore, the law requires contractors to establish clear quality control procedures and specifications for all materials and services procured from suppliers. These specifications must be communicated to suppliers in writing and incorporated into the contract. Contractors are responsible for monitoring supplier performance and conducting regular inspections to ensure that the delivered goods and services meet the agreed-upon quality standards.
In the event of non-compliance, contractors have the right to reject defective materials or services and seek compensation from the supplier. The law provides legal recourse for contractors who suffer losses due to supplier negligence or breach of contract. This ensures that contractors are protected from financial and reputational damage caused by substandard materials or services.
To facilitate supplier qualification and evaluation, the UAE government has established a centralized platform known as the Supplier Qualification System (SQS). This system allows contractors to access a database of pre-qualified suppliers who have been vetted and approved by government agencies. By utilizing the SQS, contractors can streamline the supplier selection process and reduce the risk of non-compliance.
In addition to legal compliance, ensuring quality compliance from suppliers is essential for maintaining project timelines and budgets. Substandard materials or services can lead to delays, rework, and increased costs. By partnering with reliable and qualified suppliers, contractors can minimize these risks and deliver projects on time and within budget.
Moreover, quality compliance contributes to the overall reputation of the construction industry in the UAE. When contractors consistently procure high-quality materials and services, it enhances the confidence of clients and investors in the industry’s ability to deliver safe and durable structures.
In conclusion, ensuring quality compliance from suppliers is a legal imperative in the UAE construction industry. By adhering to the requirements of the law and implementing robust supplier qualification and evaluation processes, contractors can safeguard project integrity, protect their financial interests, and contribute to the reputation of the industry as a whole.
Risk Assessment and Mitigation Strategies for Supplier Quality Issues
**Ensuring Quality Compliance from Suppliers: A Legal Perspective in the UAE Construction Industry**
In the dynamic construction industry of the United Arab Emirates (UAE), ensuring quality compliance from suppliers is paramount to project success. The UAE construction law provides a robust framework to safeguard project quality and mitigate risks associated with supplier non-compliance.
The law mandates that contractors conduct thorough due diligence on potential suppliers before awarding contracts. This includes evaluating their technical capabilities, financial stability, and quality management systems. Contractors must also establish clear quality standards and specifications in their contracts and ensure that suppliers adhere to them.
To ensure compliance, contractors can implement various quality control measures. These include regular inspections, testing, and documentation of supplier performance. The law also empowers contractors to reject non-compliant materials or services and seek compensation for any resulting losses.
In addition to contractual obligations, the UAE construction law imposes legal liabilities on suppliers for providing defective materials or services. Contractors can hold suppliers accountable for any damages or injuries caused by non-compliance. This legal recourse provides a strong incentive for suppliers to maintain high quality standards.
Furthermore, the law encourages collaboration between contractors and suppliers to promote quality compliance. Contractors can provide training and support to suppliers to enhance their capabilities and ensure they meet project requirements. Suppliers, in turn, should be proactive in communicating any potential quality issues and working with contractors to find solutions.
By adhering to the legal framework and implementing effective quality control measures, contractors can mitigate risks associated with supplier non-compliance. This not only ensures project quality but also protects contractors from legal liabilities and financial losses.
In conclusion, the UAE construction law provides a comprehensive framework for ensuring quality compliance from suppliers. By conducting thorough due diligence, establishing clear quality standards, implementing quality control measures, and fostering collaboration, contractors can safeguard project quality and minimize risks associated with supplier non-compliance. This legal framework contributes to the overall success and sustainability of the UAE construction industry.
Continuous Improvement and Supplier Development for Quality Enhancement
**Ensuring Quality Compliance from Suppliers: A Legal Imperative in UAE Construction**
In the dynamic construction industry of the United Arab Emirates (UAE), ensuring quality compliance from suppliers is paramount for project success and legal adherence. The UAE construction law places significant emphasis on quality control, mandating contractors to procure materials and services from suppliers who meet stringent quality standards.
To comply with these legal requirements, contractors must establish a robust supplier qualification process. This involves evaluating suppliers based on their technical capabilities, financial stability, and quality management systems. Contractors should request documentation such as quality certifications, test reports, and references to assess suppliers’ adherence to industry standards.
Once qualified, suppliers must be monitored regularly to ensure ongoing compliance. This can be achieved through site inspections, audits, and review of supplier documentation. Contractors should also establish clear communication channels with suppliers to facilitate timely resolution of any quality issues.
The UAE construction law also requires contractors to maintain a quality management system (QMS) that aligns with international standards such as ISO 9001. This QMS should include procedures for supplier selection, monitoring, and corrective action. By implementing a comprehensive QMS, contractors can demonstrate their commitment to quality and minimize the risk of non-compliance.
In addition to legal compliance, ensuring quality compliance from suppliers brings numerous benefits to construction projects. It reduces the likelihood of defects and rework, leading to cost savings and timely project completion. It also enhances the reputation of contractors and suppliers, fostering long-term business relationships.
Furthermore, quality compliance contributes to the overall safety and durability of construction projects. By using high-quality materials and services, contractors can ensure that buildings and infrastructure meet the required performance standards and provide a safe environment for occupants.
In conclusion, ensuring quality compliance from suppliers is not only a legal requirement in the UAE construction industry but also a critical factor for project success. By implementing a robust supplier qualification and monitoring process, contractors can mitigate risks, enhance quality, and contribute to the overall safety and durability of construction projects.
The Role of Technology in Ensuring Supplier Quality Compliance
**Ensuring Quality Compliance from Suppliers: The Role of Technology in the UAE Construction Industry**
In the dynamic construction industry of the United Arab Emirates (UAE), ensuring quality compliance from suppliers is paramount to project success. The UAE construction law places significant emphasis on quality control, mandating contractors to procure materials and services that meet stringent standards.
Technology has emerged as a powerful tool in facilitating supplier quality compliance. By leveraging digital platforms and innovative solutions, contractors can streamline the supplier selection process, monitor performance, and enforce quality standards throughout the supply chain.
**Supplier Pre-Qualification and Selection**
Technology enables contractors to pre-qualify suppliers based on their track record, certifications, and financial stability. Online supplier databases and procurement software provide access to a vast pool of potential suppliers, allowing contractors to compare their capabilities and identify those that best align with project requirements.
**Quality Monitoring and Inspection**
Once suppliers are selected, technology can facilitate real-time quality monitoring. Contractors can use mobile applications to capture inspection data, record non-conformances, and track corrective actions. This data can be centralized in a cloud-based platform, providing a comprehensive view of supplier performance and enabling proactive quality management.
**Automated Compliance Checks**
Technology can automate compliance checks by integrating with supplier systems. Contractors can set up rules and thresholds to ensure that materials and services meet specifications. Automated alerts can be triggered when non-conformances are detected, allowing for prompt corrective action.
**Supplier Performance Management**
Technology enables contractors to track supplier performance over time. Key performance indicators (KPIs) such as delivery time, quality defects, and customer satisfaction can be monitored and analyzed. This data can be used to identify underperforming suppliers and reward those who consistently meet or exceed expectations.
**Collaboration and Communication**
Technology fosters collaboration and communication between contractors and suppliers. Online platforms provide a central repository for project documents, specifications, and quality control reports. This transparency promotes open communication and ensures that all parties are aligned on quality expectations.
**Benefits of Technology-Enabled Quality Compliance**
By leveraging technology, contractors can reap numerous benefits in ensuring supplier quality compliance:
* Improved project quality and reduced defects
* Reduced rework and cost overruns
* Enhanced supplier performance and accountability
* Streamlined procurement processes
* Increased transparency and collaboration
**Conclusion**
In the UAE construction industry, technology plays a pivotal role in ensuring quality compliance from suppliers. By embracing digital platforms and innovative solutions, contractors can streamline supplier selection, monitor performance, enforce quality standards, and foster collaboration. This ultimately leads to improved project outcomes, reduced risks, and enhanced customer satisfaction.
Legal Consequences of Non-Compliance with Quality Standards in UAE Construction
Ensuring quality compliance from suppliers is paramount in the construction industry, particularly in the United Arab Emirates (UAE), where stringent regulations govern construction practices. Non-compliance with quality standards can lead to severe legal consequences, including fines, project delays, and even criminal charges.
The UAE construction law places a significant emphasis on quality control, with specific regulations outlining the responsibilities of suppliers in ensuring the quality of materials and components used in construction projects. Suppliers are required to adhere to industry standards, obtain necessary certifications, and maintain proper documentation to demonstrate compliance.
Failure to comply with quality standards can result in legal action against suppliers. The UAE construction law provides for various penalties, including fines, project suspensions, and even imprisonment in severe cases. Additionally, suppliers may face civil liability for damages caused by defective materials or components.
To avoid legal consequences, suppliers must implement robust quality control systems and ensure that their products meet the required standards. This includes conducting thorough inspections, obtaining independent certifications, and maintaining detailed records of all quality-related activities.
Contractors and developers also have a responsibility to ensure that suppliers comply with quality standards. They should conduct due diligence on potential suppliers, review quality certifications, and establish clear contractual agreements outlining quality requirements.
In addition to legal consequences, non-compliance with quality standards can also damage a supplier’s reputation and lead to loss of business. Customers are increasingly demanding high-quality products and services, and suppliers who fail to meet these expectations may find themselves losing market share to competitors.
Ensuring quality compliance from suppliers is not only a legal obligation but also a sound business practice. By adhering to quality standards, suppliers can protect themselves from legal risks, enhance their reputation, and gain a competitive advantage in the market.
Contractors and developers should work closely with suppliers to establish clear quality expectations and ensure that suppliers have the necessary systems and processes in place to meet those expectations. By fostering a collaborative approach to quality control, all parties involved can mitigate legal risks and ensure the successful completion of construction projects.
Best Practices for Collaboration and Communication with Suppliers for Quality Assurance
**Ensuring Quality Compliance from Suppliers: A Legal Perspective in the UAE Construction Industry**
In the dynamic construction landscape of the United Arab Emirates (UAE), ensuring quality compliance from suppliers is paramount for project success. The UAE construction law provides a robust framework to safeguard quality standards and protect the interests of all stakeholders.
The law mandates that contractors exercise due diligence in selecting suppliers and establishing clear quality requirements. Contracts should specify the desired quality levels, testing procedures, and inspection protocols. Suppliers must demonstrate their ability to meet these requirements through certifications, references, and previous project experience.
Furthermore, the law empowers contractors to conduct regular inspections and audits of suppliers’ facilities and processes. These inspections ensure that suppliers adhere to agreed-upon quality standards and identify any potential deviations. Contractors should maintain detailed records of these inspections for future reference and accountability.
In the event of non-compliance, the law provides contractors with legal recourse. They can reject defective materials, demand replacements, or terminate contracts with suppliers who fail to meet quality expectations. However, contractors must act promptly and provide suppliers with reasonable notice and an opportunity to rectify any deficiencies.
To foster effective collaboration and communication with suppliers, contractors should establish clear lines of communication and regular meetings. These meetings provide a platform for discussing quality expectations, resolving issues, and sharing best practices. Contractors should also provide suppliers with timely feedback on their performance and areas for improvement.
By adhering to the legal requirements and implementing proactive quality assurance measures, contractors can ensure that suppliers deliver materials and services that meet the highest standards. This not only safeguards the quality of construction projects but also protects contractors from legal liabilities and reputational damage.
In conclusion, the UAE construction law provides a comprehensive framework for ensuring quality compliance from suppliers. By exercising due diligence, conducting regular inspections, and fostering effective communication, contractors can mitigate risks, enhance project quality, and maintain a strong supplier network that supports their business objectives.
Q&A
**Questions and Answers about Ensuring Quality Compliance from Suppliers According to UAE Construction Law**
1. **Q: What is the legal framework for ensuring quality compliance from suppliers in UAE construction law?**
A: Federal Law No. 2 of 2016 on Construction Contracts and its Executive Regulations.
2. **Q: Who is responsible for ensuring quality compliance from suppliers?**
A: The contractor is primarily responsible, but the supplier also has obligations.
3. **Q: What are the key requirements for suppliers to ensure quality compliance?**
A: Suppliers must meet the specifications and standards set out in the contract, obtain necessary approvals, and maintain quality control systems.
4. **Q: What are the consequences of non-compliance with quality requirements?**
A: The contractor may reject the goods or services, demand rectification, or terminate the contract.
5. **Q: How can contractors verify the quality of goods or services supplied?**
A: Through inspections, testing, and documentation review.
6. **Q: What are the specific requirements for suppliers of construction materials?**
A: They must obtain approvals from the relevant authorities, such as the Emirates Authority for Standardization and Metrology (ESMA).
7. **Q: What are the requirements for suppliers of construction equipment?**
A: They must ensure that the equipment meets safety and performance standards, and provide maintenance and support services.
8. **Q: How can contractors manage the risk of non-compliance from suppliers?**
A: By conducting due diligence, establishing clear contractual terms, and monitoring supplier performance.
9. **Q: What are the dispute resolution mechanisms available for quality compliance issues?**
A: Arbitration, mediation, or litigation.
10. **Q: What are the penalties for suppliers who fail to comply with quality requirements?**
A: Fines, suspension of operations, or blacklisting.
Conclusion
**Conclusion**
Ensuring quality compliance from suppliers is crucial in the UAE construction industry to safeguard project quality, safety, and legal compliance. The UAE construction law provides a comprehensive framework for quality control, including supplier qualification, inspection, testing, and documentation. By adhering to these regulations, contractors can mitigate risks, ensure the delivery of high-quality materials and services, and maintain compliance with industry standards. Effective supplier quality management practices foster collaboration, transparency, and accountability throughout the supply chain, ultimately contributing to the successful completion of construction projects in the UAE.